How Atlanta companies are using technology to keep up with supply chain demands
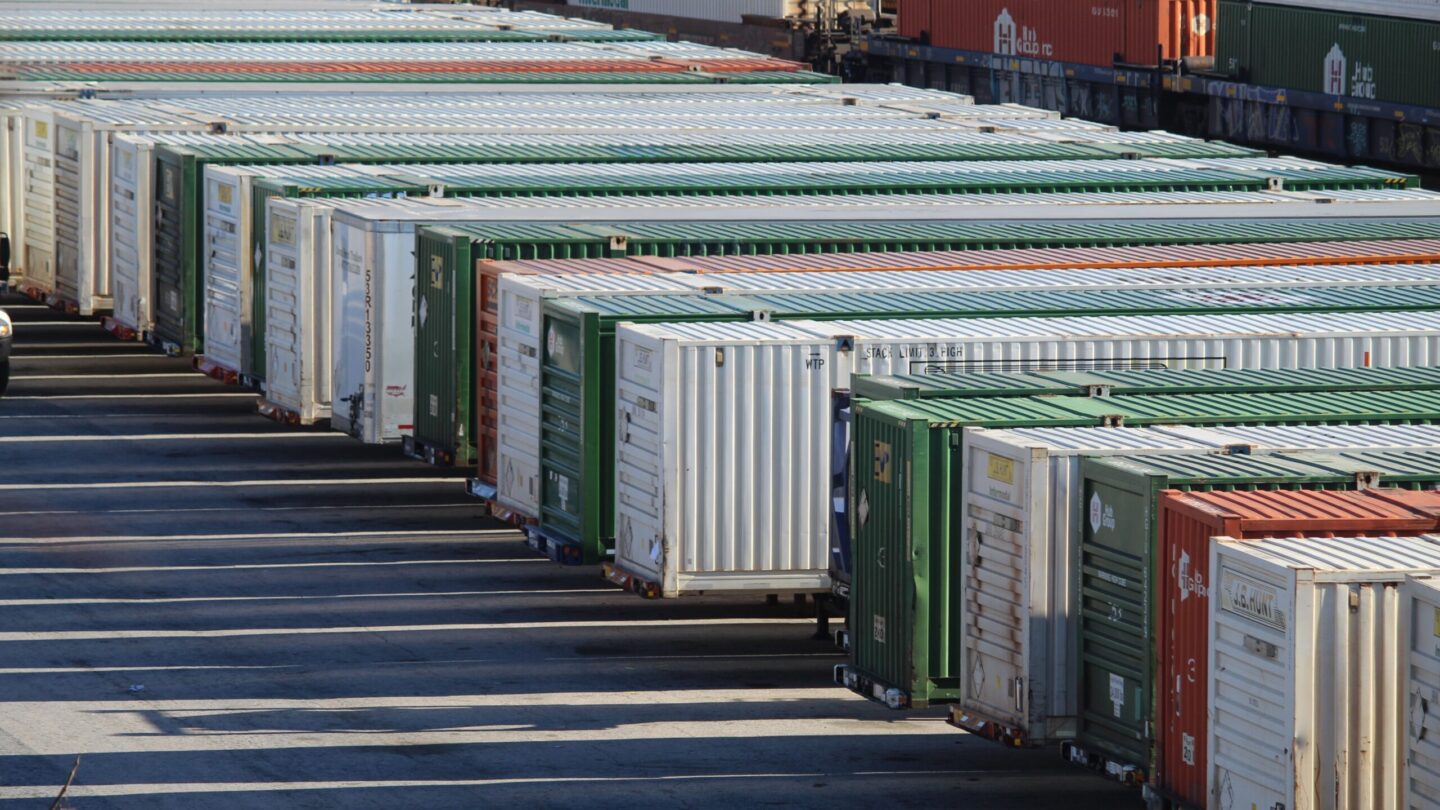
Online shopping skyrocketed at the beginning of the pandemic. And two years later, it shows few signs of slowing down.
But the increased demand has contributed to a bogged-down supply chain and left online retailers and logistics companies scrambling to keep up.
The result of this can be seen just about any day and night, on Atlanta’s west side at Norfolk Southern’s Inman Yard terminal, with semi-trucks constantly coming and going and multi-colored rows of shipping containers as far as the eye can see.
“At this facility, at Inman, we’re handling around 30,000 containers a month; Austell is handling about 50,000,” said Josh Raglin, the head of sustainability for Atlanta-based Norfolk Southern.
With more rail facilities opening at Georgia Ports, rail is seen as a key solution to moving goods without adding further congestion to highways.
‘A new normal’
The railroad industry has been around for a long time, but it also continues to be relevant and innovative. Norfolk Southern has developed technology that lets its customers calculate the most efficient way to ship their goods. It’s converting its fleet of cranes to electric-diesel hybrids and it’s also working to better integrate GPS and Bluetooth technology that will let companies keep a closer eye on where their goods are along the supply chain.
“They can get alerts. If that rail car is impacted at over seven miles an hour, they get an alert saying ‘hey someone needs to go inspect our rail car, it may have been damaged, there may have been product leaking’,” said Raglin. “They can also get an alert if that rail car’s been sitting for too long.”
Many of the technological innovations coming online these days are being spurred by record demand.
Logistics, transportation and warehousing have accounted for the biggest growth in both jobs and economic investment in Georgia over the past three years.
“We saw a tremendous explosion in e-commerce which really has created a new normal going forward,” said Sandy Lake with the Georgia Center of Innovation. “We will not be back to where we were pre-pandemic in terms of e-commerce.”
Not only has that growth been spurred by shoppers spending more time at home during the pandemic, but it’s also the result of how people shop these days, often going to their phones instead of a physical store.
“It’s really fascinating what social media has done,” said Steve Denton, the CEO of the company called Ware2Go. It’s a company that was born five years ago out of a UPS innovation lab. It uses tech to match small and mid-sized companies with warehouse space throughout the country.
He says this type of on-demand warehousing can help smaller companies compete with retail giants like Amazon.
“It connects into the order-management system, looks at where the inventory is, where the customer is and it routes that order to the warehouse that’s closest to that consumer,” said Denton.
He says with the e-commerce landscape changing as quickly as it has in recent years, having flexibility is important.
“If we started a business here in Atlanta, this would be a fine location to ship from for the East Coast,” said Denton. “But if our sales are driving in Washington State, Oregon or California, our customers, unless we’re paying for air, they’re getting a 4-5 day delivery experience.”
E-commerce fulfillment
At a spacious warehouse in McDonough, there are rows and rows of shelves filled with products from makeup to toys to home goods. This e-commerce fulfillment center is run by a company called Project Verte. The warehouse is intricately mapped out and for the last year and a half, the company has been using a fleet of robotic carts featuring cameras and sensors to help fill orders.
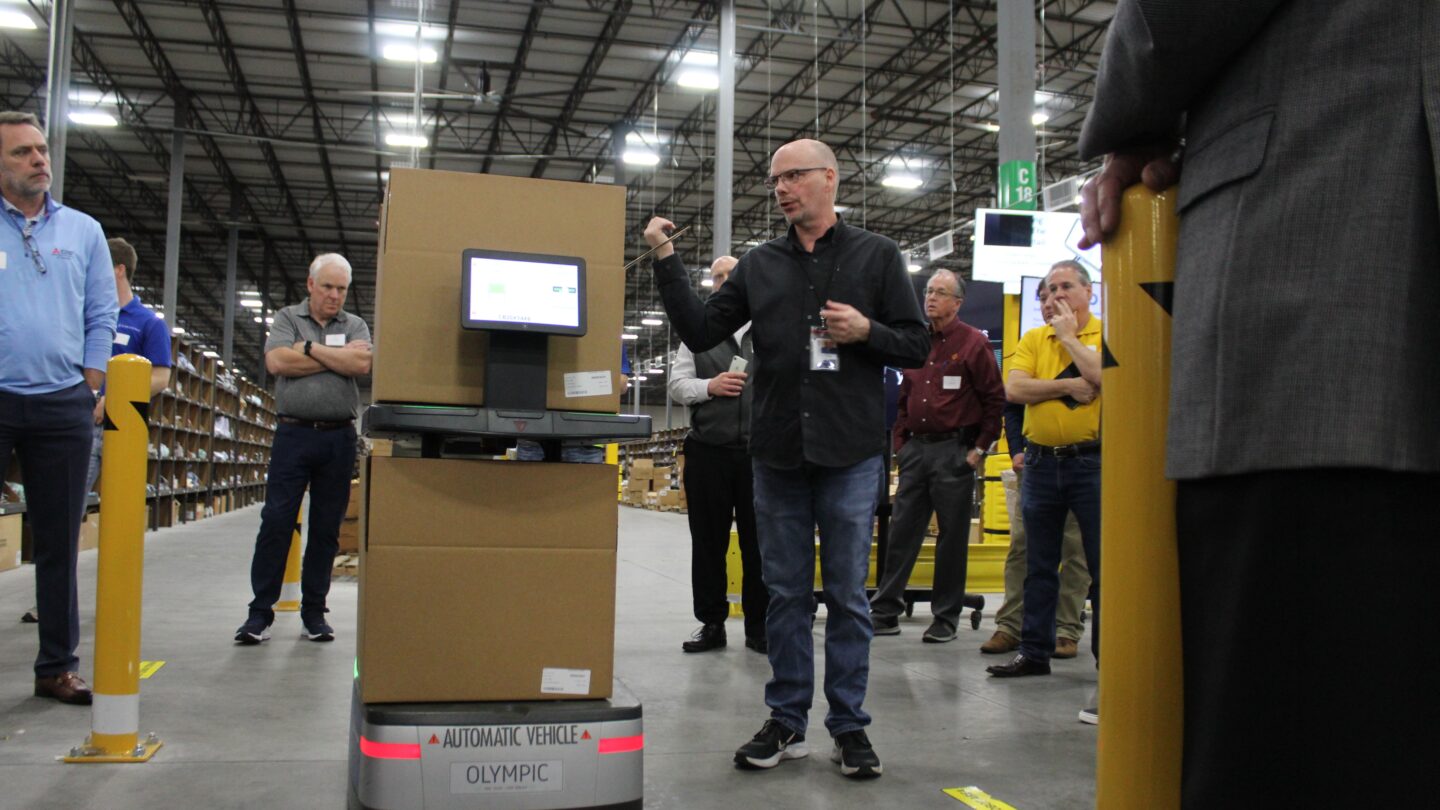
Employees scan a bar code, sending the robot to the exact spot in the warehouse where the product is located. The worker then follows behind to fill the order. Training takes just about a half-hour.
Padhu Raman, Project Verte’s chief product officer says not only do the robots save time, but they also put less physical stress on warehouse workers.
“It helps in the brand’s inventory accuracy, order accuracy, and also motivation from an associate’s perspective because they’re able to understand the process and they’re able to deliver with less fatigue as well,” said Raman.
Raman says just a few years ago, this warehouse was packing and shipping only about a hundred units a day. Now it’s up to 40,000 units per day and growing. He attributes this to the warehouse’s location – a few hours from the Port of Savannah and accessible to so much of the East Coast.
“Since it’s near to Atlanta, we’re seeing a lot of changes in micro-fulfillment – quicker, faster, same-day delivery,” added Raman. “That’s where this location has been strategic for us.”